The main evolution of the pedals with caliper concerns the working surface of the hydraulic part, which is larger than the old one.
With 6 pistons the working forces and elasticity are more realistic than with one. The crushing progressiveness and the degressive are a little bit closer to a real racing car.
.
.
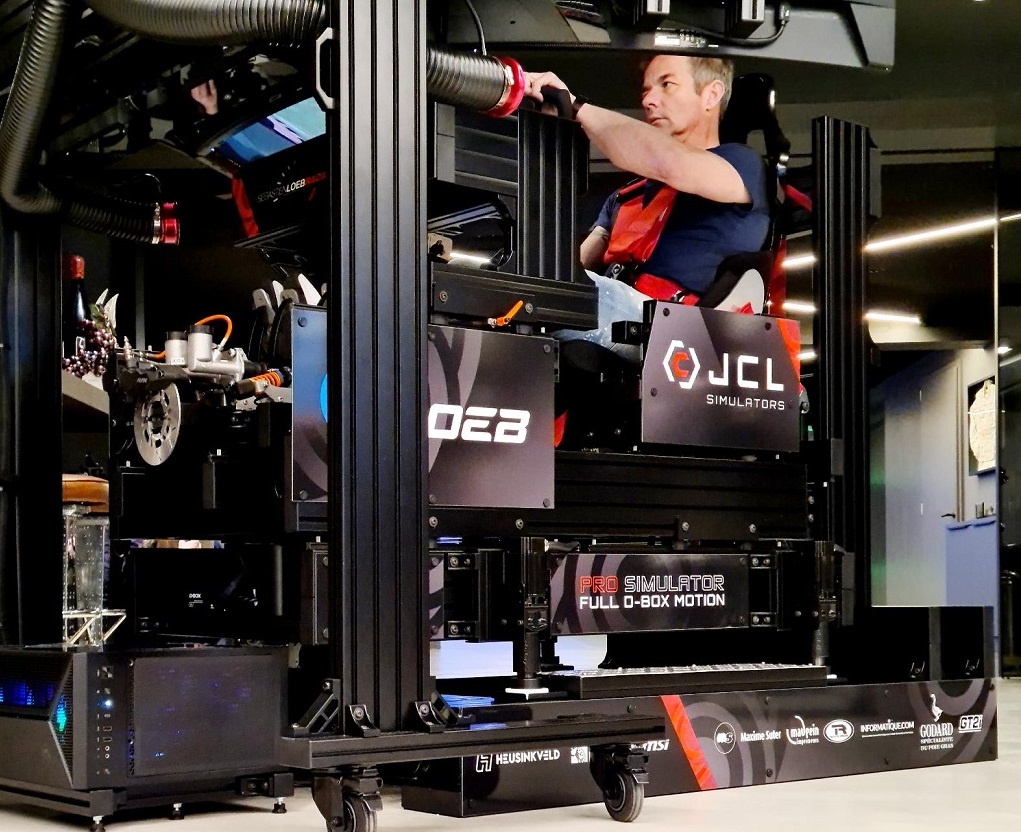
.
.
-Study and development-
- Developed in CAD by our young trainee in mechatronics engineering school,
- this new pedalboard is the result of three months of study.
- We were particularly interested in the ergonomics of the adjustment of the accelerator start/end stops and the
- We paid particular attention to the ergonomics of the throttle and clutch travel stops as well as the adjustment of the spring preload.
- All these adjustments are made manually without the need for tools or special disassembly.
- The hydraulic brake can withstand pedal pressures ranging from 65 to 110 kg. The crushing force is adjustable by means of
- by means of elastomers of different hardnesses.
- The instrumentation necessary for the acquisition of the hydraulic pressure and displacements has been entrusted to our
- electronic designer. After the in-house production of numerous 3D printing models,
- the manufacture of a first prototype required 1 month of additional work and no less than 8 months of cumulative testing both in the
- 8 months of testing, both during our presentations and in one of our clients' sports stables.
- We were also lucky enough to benefit from the expertise of the young pilot Jérémy SARHY, thanks to whom
- our product is now extremely successful in terms of realism.
.
.
-Quality materials-
- The chassis of each pedal is made of folded stainless steel sheet, previously cut by laser.
- The bead blasted finish of these parts ensures a uniform and durable appearance.
- The pedal levers and stop adjustment mechanisms are CNC machined from aerospace aluminium.
- machined from 6061 aerospace aluminium.
- Coloured surface anodising adds a professional look to these parts while protecting them from oxidation.
- Most of the screws and bolts are also made of stainless steel.
- The hydraulic braking transmitters and receivers are supplied by a famous racing brake equipment manufacturer.
- The USB acquisition card for the bottom bracket sensors is made by Leo Bodnar.
.
.
-Quality of assembly -
Just like our chassis, the assembly of each pedal is done by us in our premises and benefits from the quality
quality and expertise of JCL Simulators.
.
.
Features:
- The new JCL hydraulic pedalboard, anodised finish, stainless steel folded structures.
- Brake equipped with 2 transmitters and a Wilwood hydraulic receiver.
- Digital pressure sensor 110bars.
- Aviation hoses, Dot 5.1 brake fluid.
- Supplied with 2 pairs of pads of different hardnesses to adjust crushing pressure during braking.
- Mechanical throttle and clutch with adjustable stroke/angle of attack and compression via 3 knobs.
- Hall effect angular position acquisition. Leo Bodnar USB interface card.
- Lockable miniature industrial connectors.
- Calibration via Windows peripheral interface.
- Machined aircraft aluminium mechanisms, anodised finish, bent stainless steel pedal bracket, stainless steel screws.